Our services
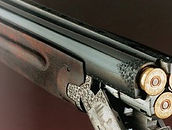
Bluing is a passivation process in which steel is partially protected against rust. The process is named after the blue-black appearance of the resulting protective finish. True gun bluing is a coating that is derived from an electrochemical conversion resulting from an oxidizing chemical reaction with iron on the surface by selectively forming magnetite. Black oxide provides minimal protection against corrosion, unless it is treated with an oil that displaces water to reduce wetting and galvanic action.
Our company has high quality tanks and chemicals for the bluing process.
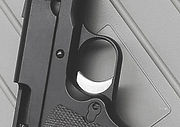
The parkerization or phosphating is a method used to protect a steel surface from corrosion to increase its wear resistance by the application of a chemical phosphate conversion coating.
Parkerization is commonly used in firearms as an alternative to bluing. It is also widely used in the automotive industry to protect unfinished metal parts from corrosion.
The Parkerization process can not be used on non-ferrous metals such as stainless steel, copper, brass ,aluminum, or steels containing a large amount of nickel.

Polishing and buffing are processes used to finish a metal surface using an abrasive, a working wheel, and several special pastes. Polishing is a more aggressive process while buffing is less harsh, which leads to a smoother, brighter finish. An erroneously accepted idea is that a polished surface has a bright mirror finish, this is a misconception, most of the bright mirror finishes are actually polished.
We have suitable machines to polish and give a mirror finish to materials such as steel, aluminum, stainless steel, brass, copper, nickel, and gold.
You can get the satin finish on any metal, giving your firearms a spectacular appearance.

Cerakote is a base Polymer-Ceramic coating that can be applied to metals, polymers and diverse materials. Cerakote is a ceramic coating and enhances a number of physical performance properties such as corrosion ,wear resistance, chemical resistance, hardness and more properties.
Magma finishing has a special section with a spray booth, oven, and spray guns for the correct application of cerakote.

Sand blasting is the process of forcing a stream of abrasive material against an object to smooth a rough surface, remove contaminants from the surface or simply embellish the surface of the material. Compressed air is used to propel the blasting material (often called the media).
There are process variants and different media types are used. Some media is too abrasive while others are softer. Moderately abrasive variants include glass blasting (with glass beads).
Our shop has two sandblast cabinets with different types of media to create different textures.
ELECTRO PLATING

Electroplating is a generally industrial process in which electric current is used to reduce the dissolved metal cations so as to form a thin coherent metallic coating on an electrode. Electroplating is used to change the surface properties of an object, such as abrasion and wear resistance, corrosion protection, lubricity and aesthetic qualities, it can also be used to add thickness to pieces of insufficient size.
Magma Finishing has electroplate system consisting of Nickel, Copper, Chrome, Electroless Nickel, and Gold.